.
What Is Cement?
In general, any kind of substance that has cohesion nature and can stick materials to each other is called cement. Adhesives in building and construction industry are mainly used to stick fine and coarse aggregates and bricks together.
The first cement-like material used by humans was clay and still remnants of old mud houses in desert areas can be found. Over the years different materials were performed as cement and nowadays various substances including cement mortar, gypsum mortar, polymer based adhesives, and etc. are accessible.
Today the most consumed kind of cement is portland cement, explained in details in this article.
.
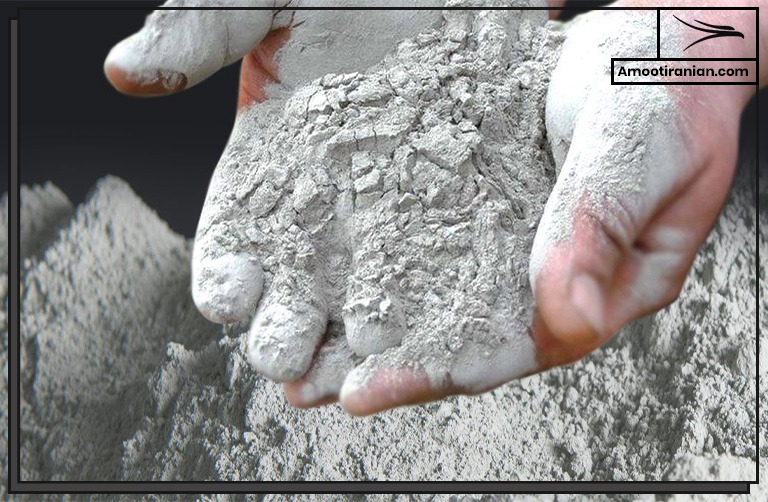
.
History of Cement
Mud cement (the first kind of cement used in the past) is not water resistant, the most significant problem of this adhesive. This caused humans to research more to discover water resistant cement and the result was sarooj.
Sarooj is a combination of lime, ash, sand, clay and loui, more water resistant compared with mud. In ancient Iran, it was used to build cisterns, reservoirs and other structures which had to be water-resistant. The invention of portland cement caused sarooj not to be used anymore.
The best kind of cement has limestone and clay in its combination. On 1824, Joseph Aspdin came to a conclusion that in order to make high quality cement, the mixture of limestone and clay should be heated and finally on 1845, Isaac Johnson created portland cement and became the pioneer of the portland cement industry.
Nowadays to make portland cement, after limestone and clay extraction from the mines and preparation, the mixture is heated to produce clinker. Then cold clinker is grinded with limestone to make portland cement powder.
It is worth mentioning that because of the resemblance of cement to portland stone (in terms of color, shape and quality), a type of building stone quarried on the Isle of Portland in Dorset of England, the name of Portland was given to cement.
.
Cement Functions
- Stick sand and coarse aggregates to each other
- Fill the distance between sand and coarse aggregates
- Makes a high density mass
.
Portland Cement Production
Generally the manufacture of portland cement has different steps but before any explanation, it is necessary to mention the two main bellow defects of cement industry:
- Very high energy consumption
- Environmental pollution
So the researchers and artisans are continuously trying to change the cement production line in a way to remove these defects as much as is feasible.
.
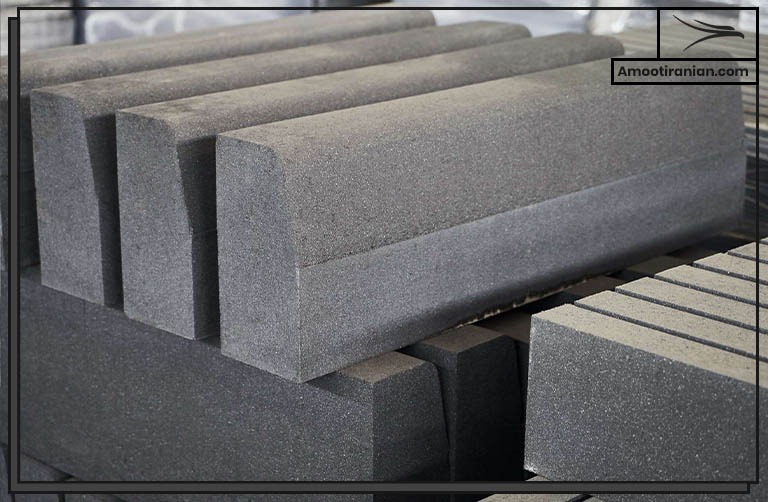
.
Where to Establish a Cement Factory?
Several issues should be considered when selecting a place to build a cement factory:
- The factory should be near the quarries of raw materials (limestone and clay)
- The selected quarries should have enough capacity to meet the cement factory requirements in long-term
- The mines should have high quality or at least acceptable quality raw materials
- The factory should be near the consumption areas
As you see, number 1 and 4 are related to the transportation costs in cement industry.
High amounts of raw materials should continuously be transferred from mines to factory and high amount of cement to the area of users so the factory must be in a place with the shortest distance to the mentioned locations.
As mentioned in number 2 and 3, an appropriate quarry, first should have good quality raw materials and second, should be able to support the required raw materials until 100 to 150 years later. Otherwise the establishment of a cement factory is not economical. As most of limestone mines of Iran are located in mountains and clay mines are also found near mountains, usually the distance between mountains is a favorable place to establish cement factories.
.
Raw Materials’ Extraction and Transfer
To extract limestone, mine blasting is needed. The intended parts of mountains are exploded with explosive materials to extract limestone rocks.
Unlike limestone, clay is extracted more easily with excavators as its quarries have low hardness. All extracted raw materials are sent to the cement factory with the help of wagons, conveyor belts or trucks.
.
Cement Transfer to Market
Cement is packaged and transferred to consumption areas in two ways:
- Bags
- Bulk
In the first way, cement is packaged in standard bags and sent to the market. Each bag should contain 25 or 50 kg of cement. Each bag has at least three layers to stop humidity penetration. Also one of these layers should be made from plastic or the distance between two layers should be covered and filled with tar. Some basic information including the company name and logo of producer, cement type, bags weight, and production date must be mentioned on cement bags with the special color related to each type of cement.
For bulk movement, trucks move cement from the factory silo to the silos of workshops. To evacuate cement from the truck to the silo, pipelines are connected to the silo, increase pressure and make airflow in the pipe.
.
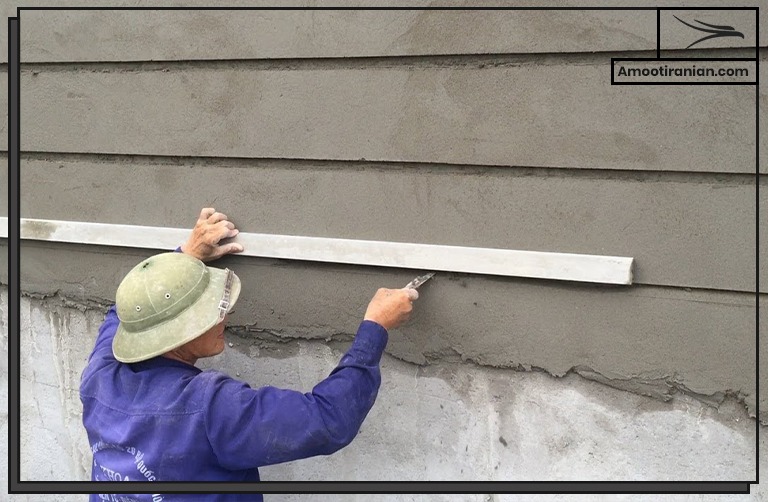
.
Cement Deterioration
Cement deterioration happens because of two bellow reasons:
- Moisture absorption from the environment (cement hydration)
- Moisture absorption from the air (cement carbonation)
To prevent cement decay in workshop, the bellow points should be regarded:
- If cement is transferred in bags, the surface of trucks where cement is moved on should be covered with plastic
- Be careful to move bags with caution to prevent any rupture
- Cement bags should be kept in covered storerooms and if it was not possible, better to cover bags with big plastics
- Never put cement bags on ground. Put them on wood surfaces that are at least 20cm above the ground
- Approximately 12 cement bags must be put on each other
- Never make mortar sooner than the usage time and more than the required amount
.
Points:
Number 1 and 3 are important to save cement from any possible rain.
The second one is related to moisture absorption.
Number 4 is necessary to protect cement bags from any water flow in the workshop. Distance between wood and ground allow air to flow and protect them from water absorption.
If you do not pay attention to number 5 and put more than 12 cement bags on each other, the underneath bags are under pressure and it causes them to become lump in vicinity of moisture. It also helps to detect any decayed bags easier and separate it from others.
Last one relates to the cement deterioration and inefficiency of mortar if the setting time is passed.
.
Cement Elements & Properties
Generally there are two levels of chemical changes in production and consumption processes of cement:
- When the raw materials have chemical interaction in furnace and burnt at a temperature of approximately 1400°C (2600°F)
- When cement and water are mixed in the process of cement hydration reaction
.
Different Types of Cement
Cement is broadly divided into two kinds of portland and non-portland. Previously, tar, gypsum and lime were the main components of non-portland cement. Hence today various kinds of polymer materials are considered as non-portland cement. Polymer materials have multiple helpful properties. However they have some particular problems. They are not fire-retardant, their properties may change in long term and the most significant point is the matter of high price.
.
Portland Cement Types of Iran
According to Iran standard that is written based on American Society for Testing and Materials (ASTM), Iran portland cement has 5 types that are mentioned bellow. The production line of all these 5 types and the required manufacturing facilities are all the same. The difference is related to the consumed raw materials and the furnace degree.
- Portland Cement (Type 1)/ Ordinary Portland Cement (OPC): It is suitable for all uses where no special properties of other types of cement are required. Ordinary Portland cement has 3 different groups:
- Type 1-325 – The minimum resistance is 325 kg/cm2 after 28 days.
- Type 1-425 – The minimum resistance is 425 kg/cm2 after 28 days.
- Type 1-525 – The minimum resistance is 525 kg/cm2 after 28 days.
- Portland Cement (Type 2)/ Modified Portland Cement: it is applied for general uses and is the most produced kind of cement in our country. It has low heat of hydration and moderate resistance against sulfate attacks.
- Portland Cement (Type 3): this type of cement gets high strength in the shortest possible time. In other words it is dried very fast while keeps its resistance.
- Portland Cement (Type 4): it is used as a low heat of hydration portland cement, when low heat of hydration in concrete is required.
- Portland Cement (Type 5)/ Sulfate Resistant Portland Cement: it is good for situations that we need high strength against sulphats in concrete. It is good for places that are exposed to sulphat attacks.